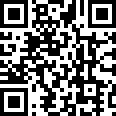
Ms. Fiona Cui
Leave a messageMs. Fiona Cui
Leave a messageCurrently, thermal spray technology in the steel industry is mainly applied to wear-resistant, corrosion-resistant and conveyor rollers spraying and welding and so on. In the iron and steel enterprises, a large number of equipment working pieces are in a high temperature, high speed, heavy load or corrosive environment, therefore, the quality and service life of these working pieces will directly affect the production efficiency, product quality and production costs of iron and steel enterprises. Thermal spraying technology is mainly used in special working conditions and surface of the working pieces that has special requirements, its typical applications such as a variety of annealing furnaces in the furnace rolls, galvanizing line of the sinking rolls, the crystallizer short edge of the copper plate, as well as a large number of hot and cold rolling process rolls. Thermal spraying rolls take part for more than 85% of all thermal spraying parts.
Thermal spraying advantages:
1. Coating improves product quality
Continuous annealing furnace rolls after use of coating surface defects reduced to almost zero. The effect on the improvement of product quality is very significant.
2. Coating improves the service life of parts and reduces maintenancecosts.
Taking the bridle rolls of the finishing mill as an example, the rolls were originally coated with hard Cr, the service life was 2.5 months. When changed to thermal spraying coating, the service life is greatly extended, and its maintenance cost rate is reduced from 1.0 to 0.2-0.1.
3. Coating can reduce production line stopping time
For example the plate shear line guide roller, after the roller using Thermal Spray Coating to strengthen, there is no wear on the roll surface, plate edge is smooth, regularly guide roller monthly average stopping time was 30 minutes now reduced to almost no stopping time, greatly reducing the stop and maintenance time.
The application of thermal spraying technology in the roll:
1. Continuous steel casting rolls
In continuous steel casting production line, the backup roller, guide roller, pinch roller and other components are often impacted by variety of stress and thermal fatigue and other factors, result large cracks in the circumferential direction of the roll surface leading to roll damage failure. After the use of self-fusion alloy to strengthen the roll surface, during use the coating produces only fine cracks with low crack propagation rates at its grain boundaries, which greatly extending the service life ofcontinuous steel casting rolls, but also prevents the occurrence of surface defects in the casting material, improve the quality of the casting material.
2. Cold rolls
The rolls (such as bridle rolls, guide rolls and straightening rollers, etc.) in the cold rolling production line are required to have wear-resistant surfaces, changes in surface roughness in the process of use needs to be small, and have constant clamping force. The rollers are generally plated with chrome, but its wear resistance is not enough, which affects the service life. After special treatment, the surface roughness changes slowly and the clamping force is becoming hard to decrease. The wear resistance of the specially treated coated rollers is 5 to 10 times greater than the chrome-plated rollers.
3. Conductive rollers
Electroplating production line tin and zinc plating with conductive rollers are manufactured by the conductive Fe type and Cu type materials and Hastelloy corrosion-resistant alloy, and plated with Ni or Cr on its surface. Due to corrosion in the plating process and the influence of wear and adhering foreign matter, etc., its service life is very short.
Electroplating conductive roller coating material should have the following properties:
(1) Conductivity needs to reach the requirements of the plating process;
(2) Corrosion and wear hard to cause changes in surface properties;
(3) The surface should be hard to attach or electrostatic accumulation of foreign matter, and even if attached is should also easy to remove.
(END)
This article is excerpted from a note on the wechat public account "Hinte coating".
Company product profile:
Luoyang Golden Egret Geotools Co.,Ltd. founded in2012,is wholly-owned by iisted company XiamenTungsten Co.,Ltd (XTC).As a backbone cemented carbideenterprise of XTC with registered capital of 1.05billionRMB and first investment of ibillion RMB,GEOTOOLSspecializes in producing and selling high quality tungstenpowder,Tungsten Carbide Powder, carbide anvils,carbideroll rings,carbidesubstrates for PDC bit,mining drill bitsand hard facing materials.
Based on decades of production experience of WC based hard-facing materials, world-class technologies and modernautomatic production lines, GEOTOOLS dedicates into development and production of high quality hard facing materialwith high hardness, best wear resistance, best corrosion resistance and application solutions.
XTC brand Thermal Spray Powder mainly includes Wc- based & Cr3C2-based. The WC coating has high hardnessdurable wear resistance, abrasion resistance, corrosion resistance and high bonding strength, mainly used in oil &gas valves, mining tools, injection screws and printing machinery parts, The Cr3c2 coating has higher thermalstability and anti-oxidation, which can be used in a high temperature and corrosive environment, e.g. inner- wall ogas pipeline and pump.
With high degree of sphericity & excellent alloy organization, cemented carbide pellet is mainly used in weldingas an additive material of PTA Powder and tubular weldina rod to improve the wear resistance of the work pieces.
GEOTOOLS provides mono-crvstalline WC-based, coarse-arain wC-based, casting WC-based and other kinds ofPTA powder. With the high quality material, most advanced production lines and word-class technologies, the PTAcoating has high hardness, durable wear resistance, high welding velocity, and low porosity characteristics. Mainlyused in Mining, Oil driling, agriculture machinery, and machining for welding and repairing.
The hard phase of GEOTOOLS tube rods is tunasten or its products with high wear resistance. Tubular welding rods aresuitable for flame brazing and widely used for surface strengthen for oil and mining drill bits.